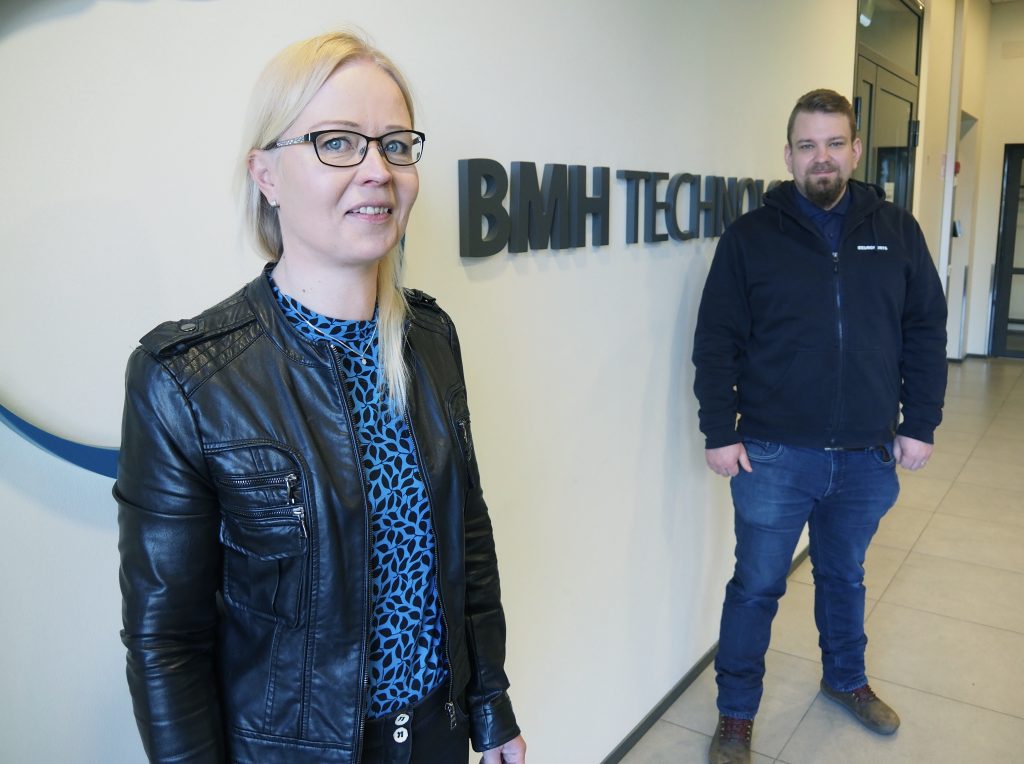
Successful cooperation is the result of a combination of factors. The partnership between Euroports Logistics and BMH Technology is based on complementary core competencies, careful planning, transparency, and continuous development. A personalised service model guarantees quick response times and extensive expertise.
Euroports Logistics handles the container cargo receipt, storage and loading operations of BMH Technology's marine export projects in Rauma. BMH Technology is a Finnish cleantech company founded in 1929. The company is a global leader in delivering demanding material handling systems and industrial-scale waste refining solutions.
“We design and deliver TYRANNOSAURUS® waste refining plants and material handling systems that produce recycled fuel from waste. We also offer maintenance services throughout their life cycle. We are a global operator with an extensive network and deliver project cargos across all continents,” says BMH Logistics Manager Johanna Valtonen.
“We aim to keep our supply chain as simple and efficient as possible, so we wanted to find reliable logistics partners that can act as our eyes and ears. Euroports Logistics was the answer, as we wanted to find a specialist in the field, able to take care of the handling and container loading of our products with the highest efficiency and quality.”
Euroports Logistics handles all BMH project cargos shipped from Rauma. Cooperation has been ongoing for about two years and has involved three large projects as well as smaller shipments. When shipping project cargos, several dozen containers may leave the port at once.
“In our projects, logistical planning begins several months before the first product is completed. This way, we ensure that project-specific requirements for sea export are clear and that products can be stored temporarily, if necessary, to make their loading easier. We start by mapping the entirety, its parts and scope, and then we plan and schedule the loading in collaboration with BMH,” says Euroports Logistics’ Business Unit Manager Tuomas Saarnilahti.
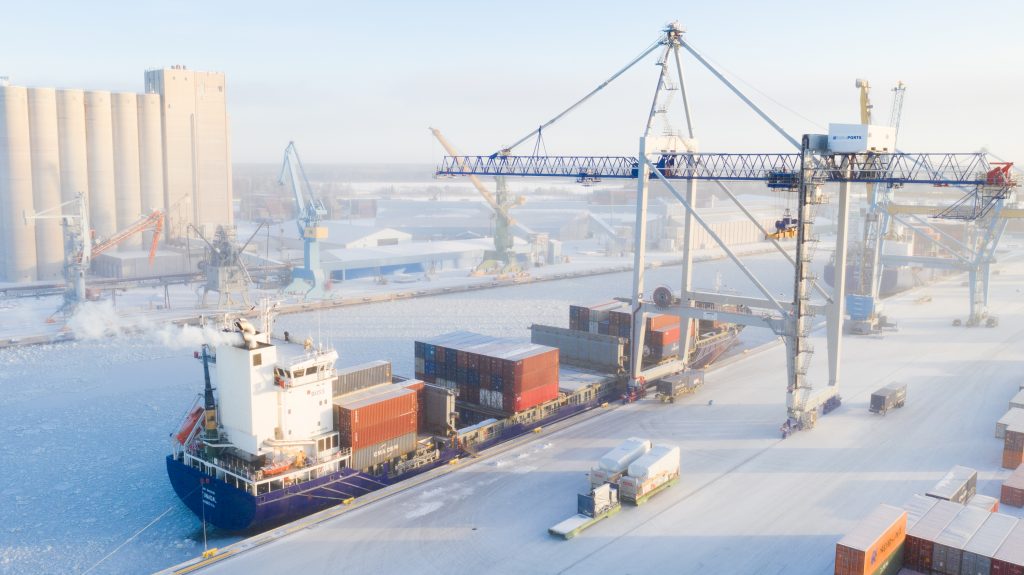
Collaboration ensures the best results
Cooperation began by mapping new containering opportunities. Based on this, Euroports Logistics tailored a service model that best suited BMH's needs.
“Previously, open top containers were largely used for product exports. We set out to find new containerisation alternatives. BMH’s products are unique and designed as part of a plant. When components are handled as individual pieces, their optimal loading requires careful planning,” says Saarnilahti.
“The careful groundwork carried out right at the beginning of the cooperation is now paying off. We received comprehensive support from BMH’s personnel who are familiar with the equipment and have extensive experience in handling it. This enabled us to build up the service model as easy as possible for them.”
The processes are described in detail. This ensures the timeliness and quality of all operations. At the beginning of the cooperation, BMH played an important role in guiding and familiarising Euroports Logistics' personnel with the specifics of the transported equipment.
“Euroports Logistics’ staff inspects the goods for any transport damage or consignment note deviations. In addition to these, a jointly defined quality inspection is also carried out, and observations and deviations are reported to BMH. The learning curve has been steadily rising during the cooperation,” says Valtonen.
“This is a good example of cooperation between two parties who complement each other with their own areas of expertise. In the early stages of the cooperation, we paid attention to issues other than their organisation had. These were found very important from a logistics point of view,” says Saarnilahti.
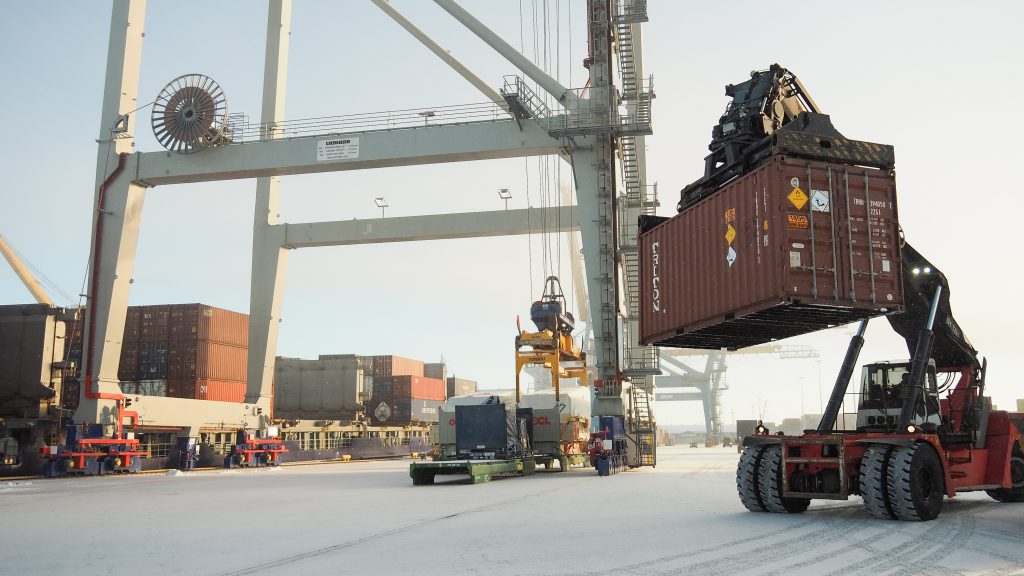
Special know-how improves cost-effectiveness
As a project progresses to the export phase, Euroports Logistics communicates the operations with Leafhill Solutions Oy, which is authorized to act as BMH's logistics department. Based on the capacity specifications determined by Euroports Logistics, they take care of freight tendering, among other freight arrangements.
“Our work begins with determining the amount of transportation units and special transportation units needed. The time scheduled for manufacturing of the various components is carefully considered when planning the loading. We receive and carry out inspections for the goods, and then take care of temporary storage before loading,” says Saarnilahti.
In terms of packaging and packaging inspections, Euroports Logistics' expertise and experience have played a significant role. The loading rate of the containers has been optimised, although changes may be made along the way if the loading rate can be further improved by arranging the products in different ways. An important part of packaging design is the rational use of packaging materials with respect for the environment.
“Euroports Logistics carefully examines how everything is packed, tied and supported so that the equipment remains intact while more than two months sea transport from Rauma to the end customer. An essential part of their planning work is to also consider the unloading of the container at the destination, taking into account the nature of the project. At our end, we ensure the quality of the equipment, and they ensure the quality of maritime logistics – so we both take care of our core competencies. We maintain a continuous dialogue and develop our cooperation together,” says Valtonen.
Euroports Logistics' efficient processes and optimal location ensure quick response times. Continuous development, on the other hand, is ensured by holding meetings to discuss the successes of previous projects and possible areas for improvement.
“The cooperation has reduced our transportation unit needs and, most importantly, enabled us to keep the need for special transportation units to a minimum. With the help of Euroports Logistics' expertise, the transported equipment now fit in a smaller space than before. By significantly reducing the number of containers, we have been able to save on freight costs and minimise the burden on the environment,” says Valtonen.
“We invest in service and quality, and they must always be at one hundred percent level. When work is meaningful and when partners value each other and each other’s work, everyone wants to give their best. This is clearly reflected in our cooperation,” says Saarnilahti.